Hertfordshire-based staging company, Brilliant Stages, was responsible for creating a set featuring the signature pronged ‘pylons’ in homage to Muse’s 2001 album Origin of Symmetry for the band’s appearances at the 2011 Reading and Leeds Festivals.
The music events take place simultaneously over the August bank holiday weekend and share the same bill, so Brilliant Stages needed to design the giant, top heavy pieces to withstand the outdoor venues and be quick to set up and take down.
The design brief from lighting and stage designer, Oli Metcalfe, was realised by Brilliant Stages’ CAD designer, David Harrison, who also acted as Brilliant’s project manager and worked closely with Muse Production Manager, Steve Iredale, in delivering the various elements.
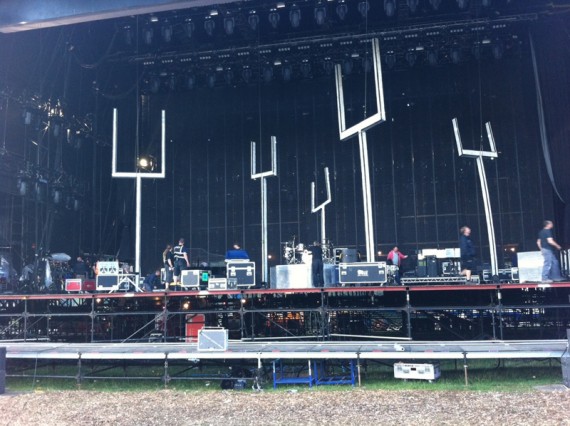
The set comprised of five forked ‘pylons’ ranging from 9.5m in height with a 2.5m wide span, to the smallest at 5.8m high – two of which were also designed to curve forward and sideways to replicate the hand-drawn perspective of the original artwork.
“Because the pylons were only going to be used at the two festival sites, we were able to maximise the structural integrity of the pieces which were very large,” explains Harrison. “The largest pylon weighed in at 250kg with most of the weight in the base for stability and security.”
Each pylon’s central mast was constructed from laser cut profiled aluminium plate welded together to form a box section and fabricated in several lengths in accordance to the limitation of aluminium sheet sizes.
The prongs of the pylons were formed of two L-shaped pieces of similar profiled aluminium box sections, which were bolted onto the central masts and could be removed for easy transportation.
To the base of each central mast were added two aluminium base plates which, in turn, were bolted and welded to a steel base plate affixed to a pivotal spike protruding from the bottom. This spike pierced the stage and was secured into a complex clamping assembly mechanism below stage level to give rigidity and precise alignment. This construction had the double benefit of adding an extra layer of safety whilst allowed the pylon to be rotated into position.
The below-stage clamp assembly was designed for both strength and versatility. A central aluminium tube was located within a steel support cradle with two nylon support clamps securing it at top and bottom. A series of half couplers then enabled the whole assembly to move both horizontally and vertically to any point within each 8ft bay beneath the stage. This allowed complete flexibility to fine tune the alignment of each pylon above stage.
The pylons were deployed by attaching the prongs to the central masts and lifting the whole assembly with hoists, before lowering them into position and clamping them into place. The only exception was the largest mast which, for speed and safety, was preset in the roof and lowered in using hoists.
Brilliant Stages also constructed the roll drop system for the band’s front reveal at the top of the set.
Ten 4mm tension cables – plastic coated to prevent snagging – were located at 2.5m intervals across the 24m wide drape and clipped off at 500 centres by retaining ‘S’ hooks. This ensured there was no slack as each fold only traveled 250mm and the drape would fold up neatly, even in the windy conditions of Reading Festival.
A header panel – composed of six 3m wide by 2.4m high painted plywood panels – concealed the drop in its ‘up’ position from the audience. This was suspended from box aluminium frame which housed the cable reeler. A series of ‘F’ shaped supports provided sufficient leeway to allow it to be positioned at any point along the truss without falling foul of the struts. This made installation easier and faster.
“From the moment we sat with Brilliant’s Tony Bowern in LH2, and discussed Oli’s design ideas, the project advanced seamlessly,” says Iredale. “Brilliant grasped the concept immediately, and came back to us within 10 days with various construction ideas. Leeds and Reading use virtually identical stages, so the structural elements of these stages were extremely important in finalizing the detailing of what became known as the ‘Goalposts’, and the reveal system. I had Serious Stages provide a complete scaffolding deck structure, which was setup at Brilliant’s premises so the construction process could be done on a physical structure as well as on the drawing board.
“Rick Worsfold, Muse’s head carpenter, spent a couple of days at Brilliant to familiarise himself with the pieces, before we started rehearsals in LH2. The first setup went seamlessly, which is seldom the case, and when the time came to finally load in the shows, any concerns that the promoter or ourselves may have had using such large elements and setting up in 30 minutes were never a problem. The end result looked fantastic and, even with high winds in Reading, the 21 meter wide by 12 meter high reveal drape at the top of the show proved to be faultless with the system constructed by Brilliant.
“As a production manager, it was a pleasure to work with Brilliant on this project, they took Oli’s idea, and built us a very large, but smart set for a festival setup”
Leave a Reply