Rigging specialist Summit Steel continued its association with hugely successful UK pop band, Take That, supplying motors, rigging and a Kinesys K2 automation system for the band’s summer “Circus” stadium tour.
Summit also provided specialist rigging consultancy, and custom designed and developed a lifting system for one of the show’s most spectacular movement cues that creates a massive WOW factor near the top of the show and involves moving a large set piece weighing 6.5 tonnes.
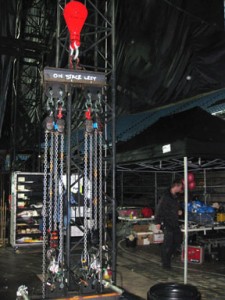
Summit’s Senior Project Manager Chris Walker worked closely with production manager Chris Vaughan from The Production Office and with the tour’s head rigger Phil Broad. “This element was easily the biggest challenge for us,” says Walker who was involved right from the early design and concept stages, and worked on it since last September.
The band started the show on the B stage, whilst a large circus tent set piece was in-situ on the main stage. Built by Brilliant Stages the eaves of the tent was a 15 metre diameter circular truss with fins reaching down, finishing just before the ground. The back of the circle was attached to 2 giant hydraulic hinges, each weighing 2.5 tonnes – while the rest was supported by four 16mm steel wires run off at 45 degree angles to four of the upstage StageCo towers.
Each of the four wires was fed through a diverter pully rigged in the towers, all double purchased. Each wire was then pulled by a rocker-beam attached to the pulley. Beneath each rocker beam were 2 quad-reeved CM Lodestar model LL hoists, all wired for the Kinesys Elevation motion control system.
At the cue point, the covering cloth was speedily removed from the tent structure. The eight hoists all pulled together to lift the circle – (complete with integral lights rigged in the trussing) as it hinged out and up, transforming into a vertically orientated frame for the large upstage centre LED screen. The set was designed by Es Devlin, based on an idea conceived by the show’s artistic director, Kim Gavin.

This very elegant move took 5 minutes and the smoothness and pinpoint accuracy of the Kinesys system came into its own. “We’re used the system in a somewhat idiosyncratic set up,” says Walker, “And once again it’s proved dynamic and versatile, enabling us to achieve the desired results”. He also adds that being involved in the design process from the start made a huge difference in how efficiently Summit was able to produce an inventive and reliable solution for a demanding and impressive piece of visual theatre.
The whole system was built and tech’d in Hangar 1 at Cardington Airfield (famous for housing the R100 and R101 airships) whilst performer rehearsals took place simultaneously on the George Lucas Stage at Elstree Studios. Full rehearsals then took place at Cardington before moving to Sunderland’s City of Light Stadium.
The Kinesys K2 system was operated by Gareth Williams. Summit also used its new Kinesys Libra load cell system, linked directly to K2 to monitor the lifting operation.
Additionally, Summit supplied over 100 Lodestar hoists to the tour – a combination of half, 1 and 2 tonne versions – which were utilised for rigging PA (Capital Sound) and video (XL Video & CT).
Summit has been involved with Take That’s well known ambitious rigging requirements since the band first rose to fame in the 1990s, and has continued to supply rigging, automation and expertise to all the subsequent tours following their meteoric comeback in 2006.
Leave a Reply